The preferable technology for local repairs is Pulsed Laser Welding. Due to key qualities that negate the need for other Technologies.
KEY REQUIREMENTS FOR A SUCCESSFUL TOOL REPAIR
- MINIMAL HAZ (Heat Affected Zone) – This means that the hardness of the surrounding area of the repair is unaffected by the weld. Resulting in no change to the desired qualities of the material. This becomes important when repairing critical mould surfaces. Where the Polish or Texture of the repair must perfectly match its surrounding areas.
- ACCURATE WELD DEPOSITION – The accuracy of Pulsed Laser Welding enables us to build even complex shapes with total control. Resulting in having less material to remove after the weld repair. This can have a cost saving during the post weld machining operations. Especially Spark Erosion. Where the minimum build can on occasion negate the need for Roughing Electrodes.
- ULTRA LOW DISTORTION – The resulting minimal heat affected zone after a pulsed welding operation allows Carrs to repair thin profiles with little or no distortion. Something that is almost impossible for technologies such as TIG Welding. Small chips on blades or tiny upstanding core features are regular occurring Laser repairs for this very reason.
- ACCESSIBILITY TO DIFFICULT AREAS – Pulsed Laser Welding is a line of sight operation through a narrow conical angle (30° inclusive). This allows access to areas that even the smallest TIG Torch would fail to reach, combine this with the concentrated energy of the Laser and areas such as pockets, slots and acute-angled faces can now be accurately welded where they once would be inaccessible or require opening-out to gain access operations prior to the repair action.
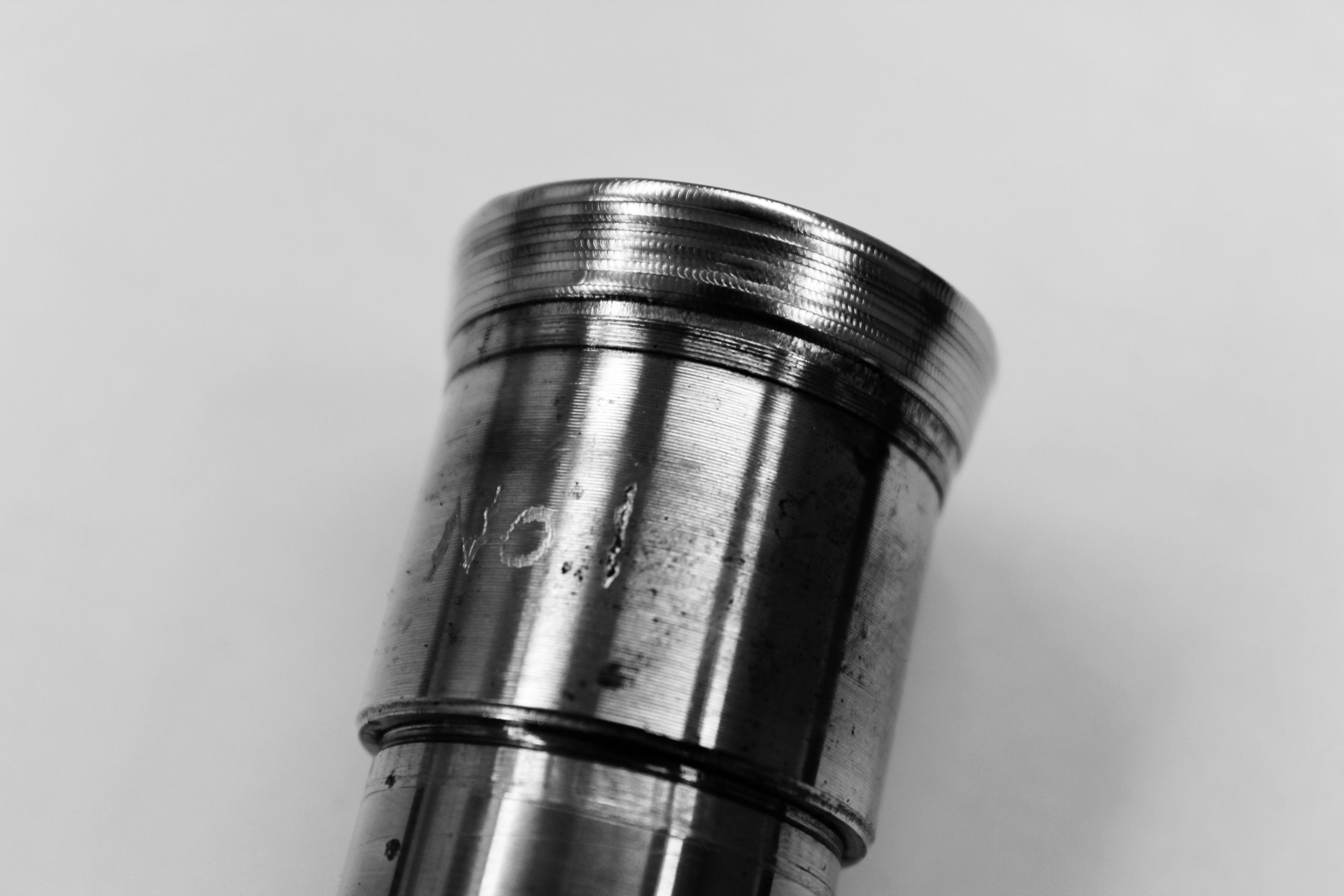
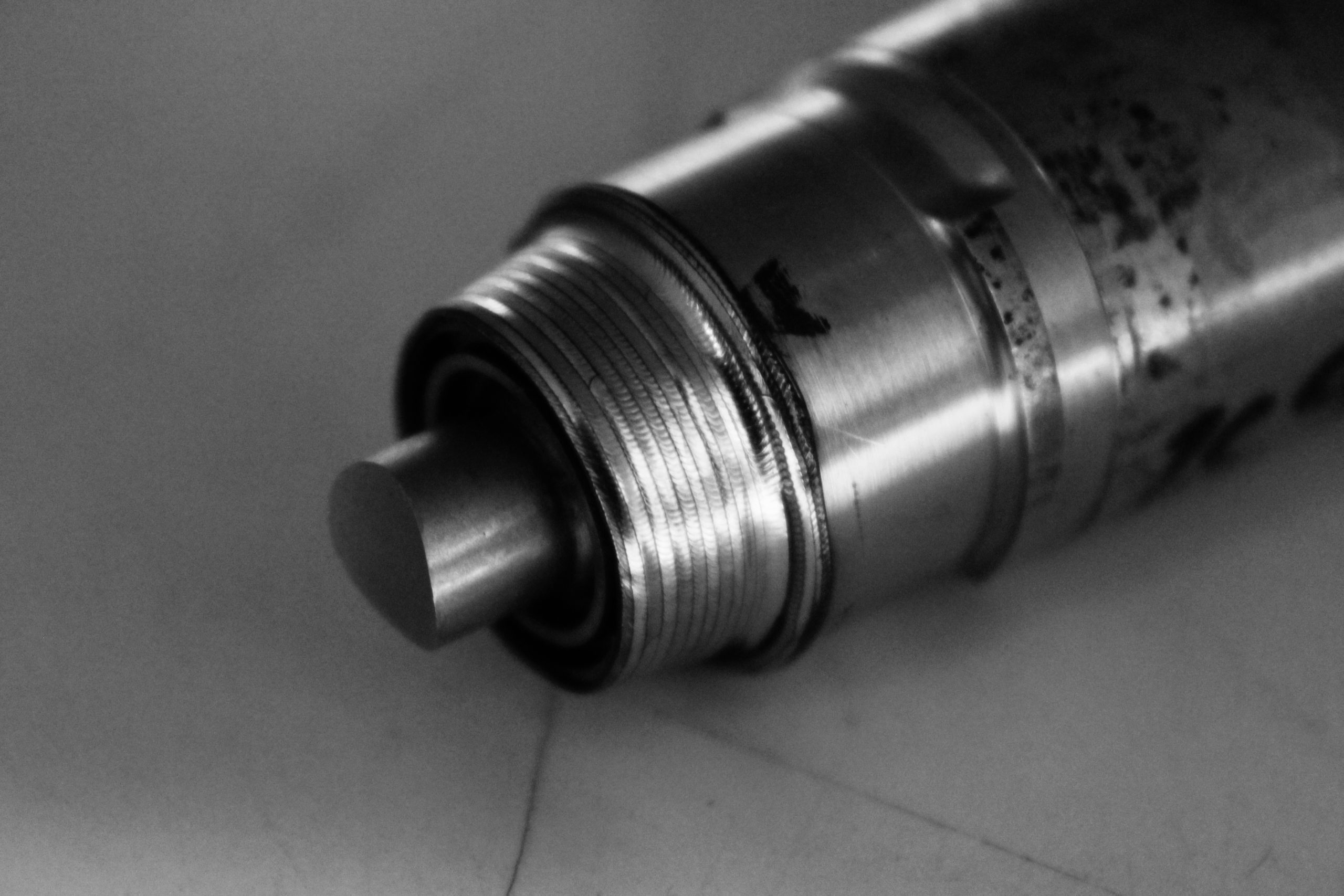
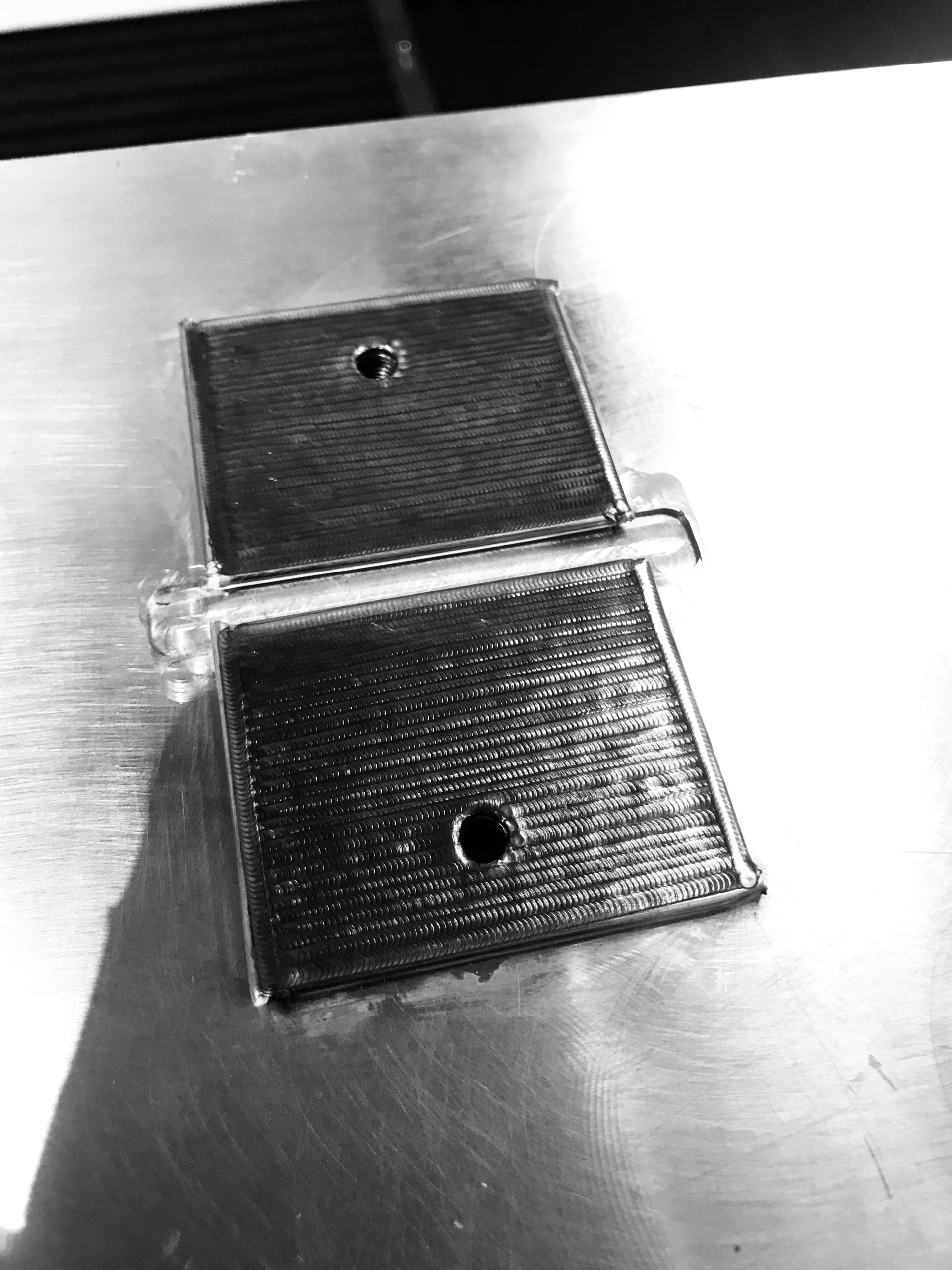
There are still occasions where technologies like TIG Welding are the right choice, which is why Carrs offers both Laser and TIG services and will always look to provide the best option for each application.
It is worth knowing that every repair operation will require the addition of filler material. Carrs will assess the best filler material to be used based on its customers’ requirements, which include, resistance to wear and tear, hardness, high-temperature resistance, thermal and electric conductivity, among others.